Colhedora
Automotriz Convencional
Uma colhedora automotriz
convencional é constituída basicamente dos seguintes sistemas ( figura 1)
1) corte, recolhimento e alimentação; 2) trilha; 3) separação; 4) limpeza; 5)
elevação de retrilha; 6) elevação de grãos trilhados e; 7) armazenagem e
descarga. O sistema de corte, recolhimento e alimentação (Figura 2) possui os
seguintes componentes e respectivas funções: barra de corte (1) -tema função de
realizar o corte das hastes das plantas. É “constituída de navalhas,
contra-navalhas, dedos duplos, régua e placas de desgaste.; molinete (2)- tem
a função de tombar sobre a plataforma as plantas cortadas pela barra de corte. É então foto suportes laterais, eixo e pentes
recolhedores e necessita de velocidade e posicionamento adequados; caracol (3)
- é um cilindro situado na plataforma logo após a barra de corte, tendo na
sua superfície e a partir das extremidades, lâminas helicoidais que trazem para
o centro da plataforma todo o material cortado pela barra de corte e que cai
sobre a plataforma. Na parte central, o caracol possui uma série de dedos
retráteis os quais ficam totalmente expostos na parte da frente do caracol,
transferindo o material amontoado pelos helicóides para a esteira alimentadora:
esteira alimentadora (4) - é um mecanismo constituído de duas transmissões por correntes
paralelas, unidas por travessas que preenchem totalmente o espaço, também
conhecido por garganta, que une a plataforma de corte ao sistema de trilha.
O sistema de trilha (Figura 3) é
constituído dos seguintes componentes: cilindro de trilha (1) - composto de
barras estriadas dispostas sobre uma estrutura metálica em forma de cilindro.
Tem a função de exercer ações mecânicas de impacto, compressão e atrito, por
esfregamento, sobre o material que está sendo introduzido entre ele e o
côncavo, causando a trilha; côncavo (2) - tem a forma aparente de uma calha
tendendo a envolver o cilindro de trilha. É composto de barras estriadas unidas
por estrutura metálica que toma forma de uma grelha que permite a filtragem das
sementes, vagens e fragmentos de vagens e de hastes. O material não filtrado
através do côncavo é dirigido ao sistema de separação.
O sistema de separação (Figura 3) é composto
de: extensão regulável do côncavo (3) - suspende o fluxo de palha e grãos, de
forma que o batedor direcione o mesmo sobre o extremo dianteiro do saca palhas,
aproveitando assim, toda a área de separação. Sem a extensão do côncavo, a
maior parte do material trilhado cairia sobre o bandejão, indo posteriormente sobrecarregar
as peneiras. Com a extensão do côncavo, espera-se que apenas os grãos soltos
caiam sobre o bandejão. batedor (4) - tem a função de reduzir a velocidade da
palha eliminada pela abertura de saída do sistema de trilha e direcioná-la para
a parte frontal do saca palhas, realizando ainda uma batedura final da palha
graúda para a liberação de sementes eventualmente não separadas; cortinas
retardadoras (5) - geralmente feitas de material flexível (lona ou borracha), estão
situadas sobre o saca palhas e têm a função de retardara velocidade de eliminação
da palha, para garantir a filtragem dos grãos misturados à mesma: saca palhas
(6) - têm a função de eliminar a palha graúda e recuperar as sementes misturadas
à mesma. É composto feio raramente de 4 a 6 calhas perfuradas, com grelhas no seu
interior para a recuperação e escoamento das sementes e com as bordas em forma
de cristas voltadas para a parte traseira para eliminar a palha graúda.
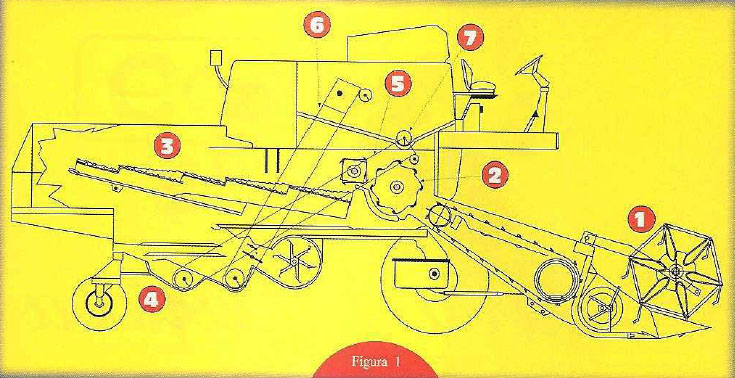
O sistema de limpeza (Figura 4) possui os
seguintes componentes: bandejão 1) - é uma superfície em forma de crista alternando
partes inclinada se verticais) voltada para a parte posterior da colhedora, situada
abaixo do côncavo c que possui um movimento retilíneo de vaie- vem. Às
partículas mais pesadas, no caso as gementes, ficam embaixo, e as partículas
mais leves, o palhiço, em cima.
Na parte final do bandejão, um pente de arame
facilita a separação dos grãos e da palha, auxiliado pela corrente de ar do” ventilador,
quando as camadas estratificadas são atiradas sobre as peneiras; peneira superior
(3) - é uma peneira de abertura ajustável e que possui também um movimento
de vai-e-vem. Recebe o material vindo do bandejão e tem a função de
filtrar os grãos. Pelo movimento de vai-e-vem as vagens inteiras devem
ser transportadas até a parte posterior da peneira onde passarão à
extensão da peneira superior, que possui abertura um pouco maior do que a
peneira inferior.
Nesta extensão, as vagens inteiras e
pedaços de vagens ainda contendo sementes, serão filtrados e dirigidos
novamente ao mecanismo de trilha; peneira inferior (4) - é uma peneira similar à
superior, devendo ter sua abertura ajustada para permitir somente a passagem de
grãos. ventilador (2) - tem a função de gerar uma corrente de ar ascendente que
age por baixo das peneiras eliminando todas as partículas mais leves que as sementes. O sistema de elevação de retrilha (Figura 4) é basicamente
composto dos seguintes componentes: sem fim da retrilha (1a) - é um eixo
helicoidal, situado na estrutura da colhedora em posição transversal e abaixo
das peneiras. Tem a função de conduzir o material não trilhado para o elevador de
retrilha; elevador de retrilha (2a) - situado geralmente na lateral direita da
colhedora, tem a função de transportar para o mecanismo de trilha as vagens
inteiras e pedaços de vagens contendo sementes que foram filtrados pelo côncavo
mas não pelas peneiras.
O sistema de elevação de grãos trilhados
(Figura 4) tem os seguintes componentes: sem fim da trilha (1b) - é um
eixo helicoidal, similar ao da retrilha, também situado abaixo das peneiras, e
que tem a função de transportar os grãos trilhados lateralmente para o
elevador de grãos trilhados; elevador de grãos trilhados (2b) - geralmente também
situado na lateral direita da colhedora, tem a função de elevar os grãos
trilhados, que foram filtrados pelo côncavo e pelas peneiras, para serem depositados
no tanque graneleiro TO.
O sistema de armazenagem e de descarga é
composto pelos seguintes elementos: tanque graneleiro - é o depósito da
colhedora onde são temporariamente armazenados os grãos colhidos durante o
processo de colheita descarga - é um tubo cilíndrico que possui um eixo
helicoidal no seu interior e que é articulado e acoplado ao sem-fim do tanque graneleiro
para a realização da descarga do mesmo.
Levantando Problemas, Colhendo
Soluções
Momento culminante do processo agrícola,
a colheita justifica uma abordagem crítica, que ponha em xeque conceitos
tradicionais, proporcionando uma espécie de mea culpa por parte dos segmentos
envolvidos — produtores e fabricantes de máquinas e implementos. Onde e como o
setor industrial tem pecado ao não oferecer alternativas e inovações, e de
que forma os produtores têm falhado ao manterem uma estrutura produtiva não- -
profissional, incompatível com os! avanços tecnológicos de um mundo globalizado?
A colheita começa pela máquina
Na esteira desse conceito, que apesar
de verdadeiro, apresenta sutilezas que não podem ser ignoradas, muitos
produtores aventuram- se na decisão, por vezes precipitada, de adquirir seu
maquinário próprio, sob o pretexto simplista de não tornarem-se dependentes de
terceiros, mas, em muitos casos, tornando-se reféns do sistema bancário.
A decisão de adquirir uma máquina só
deve prevalecer quando a relação custo-benefício a justificar. A advertência
vem dos próprios fabricantes. O diretor executivo da AGCO do Brasil (Massey Ferguson),
engenheiro agrícola Paulo Hermann lembra que não é recomendável se adquirir uma
colhedora sem que se disponha de. uma área adequada para diluir o seu custo.
“Com um uso restrito, de 400/600 horas anuais não há como amortizar esse
investimento”, argumenta.
Além disso, em tempos de economia estabilizada
como o que estamos vivendo,deve-se minimizar, sempre que possível, os
investimentos em ativos fixos , privilegiando o capital de giro. A solução pode
passar, então, por um sistema de contratação de serviços. Mas aí, a falta de
uma cultura favorável à utilização de trabalho terceirizado e a ineficiência
dos prestadores de serviço configuram um problema a ser solucionado pelas partes envolvidas. De um lado, os produtores precisam rever conceitos
tradicionais, pois não há mais espaço para aquisição de máquinas e outras
decisões, levadas por fatores como status e medição de forças entre
proprietários rurais. E de outro, os eventuais prestadores de serviços devem
buscar a profissionalização de sua atividade, equipando a honrar os
compromissos assumidos.
Máquinas
modernas, implementos ultrapassados
Outra realidade que não pode ser
esquecida é a de que mecanização não pode ser vista como máquina agrícola.
“Mecanização é sistema”, adverte Paulo Hermann, citando como exemplo um: trator que,
isoladamente, de nada vale — só tem uma função quando, acoplado a um
implemento, realiza um trabalho.
O problema é que, enquanto os tratores e
colhedoras se globalizaram (100% das colhedorase 95% dos tratores, estão sob o
controle de grupos internacionais), tornando disponíveis ao agricultor as mais modernas
tecnologias existentes em nível mundial, o mesmo não acontece com os
implementos, que continuam nas mãos de empresas familiares, sem acesso às novas
tecnologias e com mercado restrito apenas ao nacional.
Esse fato coloca o produtor em confronto
com dois mundos: máquinas com grande aparato tecno- | lógico, gerando
informações muito ricas, e implementos ultrapassados, que não permitem
operações como aplicações localizadas de fertilizantes, fluxo variável de
distribuição de sementes, entre outros.
As máquinas vão à luta
A cultura está no ponto, o tempo está firme, mas tem início a ciranda de
máquinas quebrando. Esse problema, comum em muitas propriedades, acaba
comprometendo o resultado da colheita. Segundo Paulo Hermann, esta realidade tem
causas bem determinadas: manutenção inadequada ou máquinas com idade elevada.
Uma frota com idade média corresponde
a um parque de máquinas onde 50%são máquinas pequenas — de três a quatro saca-' palhas.
Como a máquina pequena tem um desempenho baixo, ela vai! para o trabalho
antes que a cultura esteja totalmente pronta, passa pelo período ideal termina
quando a cultura já está passada do ponto- o que, em culturas como a soja, é um
terror.
Já o problema da idade elevada da má: quina
implica na falta de peças originais, abrindo espaço para as “emjambrações”, as
adaptações e ao canibalismo entre máquinas — desmonta-se duas para fazer uma, às
vezes de marca ou modelo diferentes, com resultados previsíveis.
“Máquina bem conservada, trabalhando um
número pequeno de horas anualmente, é equipamento que trabalha dez anos sem
problemas. Mas máquina mal conservada, com idade de 15-18 anos, está sempre no
limite. Máquinas pequenas, má conservação, idade elevada, e a necessidade de
colher em um curto prazo, são componentes que exigem um programa de permanente
atualização da frota”, enfatiza Hermann.
A profissionalização do processo Merece
também ser enfocada a não-correspondência entre o que se investe em tecnologia
e o uso que se faz dessa tecnologia. O investimento que se faz na aquisição de
uma colhedora pressupõe uma utilização correta, com operadores treinado se lavouras
adequadas.
“Muitas vezes, O que se vê é esse
equipamento, com alto grau de sofisticação tecnológica, operando dentro de uma
estrutura produtiva não-profissional, amadora, com operadores mal qualificados
e lavouras mal conduzidas, comprometendo todo o resultado do investimento”,
comenta o executivo da AGCO.
Assistência técnica
Como exemplo de assistência técnica à colhedoras utilizou-se a empresa
SLC—John Deere que possui uma rede de concessionários distribuída em todo o
Brasil, treinada para realizar o atendimento técnico aos, clientes de sua área
de atuação. Além desta, rede, a fábrica possui uma equipe de instrutores e
consultores técnicos, que realizam visitas e apoio técnico a clientes.
Anualmente, também são oferecidos aos concessionários programas dirigidos a
clientes e que objetivam, principalmente, maximizar o desempenho dos
produtos e satisfazê-los com os serviços de pós-venda. Osipro-. gramas
oferecidos na aquisição de colheitadeiras são:
Curso de Operação
Objetivam ensinar e orientar
principalmente sobre: segurança, operação, regulagens e manutenção, visando o
máximo desempenho dos produtos. Proporcionar treinamento aos clientes e
seus operadores, “para que obtenham conhecimento sobre os produtos, através dos
cursos de operação, “organizados pelo concessionário e ministrados consultores
técnicos ou instrutores do departamento de serviço da empresa junto ao
concessionário. Os cursos de operação são promovidos pelo concessionário,
todavia, a empresa se propõe a ministrá-los.
Boa Colheita - Esse programa é
realizado especialmente para clientes no período de colheita. Durante sua
execução, a empresa presta suporte técnico ao concessionário, colocando à sua
disposição consultores técnicos do departamento de serviço, durante um determinado
número de dias, para visitar clientes no período de maior utilização dos
produtos nas propriedades, objetivando solucionar possíveis problemas
mecânicos, de operação, regulagens, informar como obter melhor desempenho e descobrir
novas necessidades dos clientes. O concessionário deve selecionar os clientes
que deseja visitar, disponibilizando um profissional de serviço treinado na
fábrica, e preparar o ferramental necessário a ser utilizado.
Visita 5 Estrelas
O programa é dirigido a clientes frotistas,
possuidores de quatro ou mais produtos, tendo como principal objetivo dar uma
atenção diferenciada para esses clientes, através de um treinamento
personalizado à sua equipe, visando fortalecer a parceria e mantê-los satisfeitos com os produtos e serviços da SLG — John Deere. O
programa é executado na propriedade do cliente, com a participação do mesmo e
de seus profissionais, e tem duração de um dia (8 horas).