
Colhedoras de Fluxo Axial Reduzem Danos às Sementes
Edição VII | 04 - Jul . 2003 Sendo a colheita a última etapa dentro do
processo produtivo, nesta fase todos os investimentos e esforços para alcançar-se
um bom rendimento da lavoura foram executados, faltando apenas a retirada do
produto. Inegavelmente, as colhedoras automotrizes são muito importantes na
execução da tarefa de retirada do produto acabado da lavoura (colheita).
Nesta operação, faz-se necessário, além de
um adequado e cuidadoso planejamento, um correto conhecimento das
características do produto a ser colhido e da máquina a ser utilizada. Fatores
como umidade dos grãos, uniformidade da lavoura e habilidade do operador são de
grande importância para o adequado controle das perdas, que poderão ocorrer
durante a operação de colheita, garantindo o sucesso ou fracasso desta fase.
A umidade das sementes influencia, diretamente, a operação de
trilha, pois cada cultura apresenta uma faixa de umidade na qual essa operação
dá-se de forma ideal. Como é impossível efetuar- se toda a colheita com as
sementes na umidade ideal de trilha, visto ocorrerem limitações tanto de ordem econômica
quanto de capacidade operacional da frota de máquinas, normalmente, a colheita
é iniciada com as sementes apresentando umidade acima dos níveis considerados
ideais. Também se deve levar em conta que a umidade das sementes decresce ao longo
do dia, fazendo com que muitas vezes haja necessidade de estabelecer- se uma
nova regulagem na colhedora.
A uniformidade na maturação das sementes em uma mesma planta e, conseqüentemente,
a sua umidade é um aspecto a ser considerado. Deve-se dar preferência à
utilização de variedades que proporcionem uma maturação uniforme. Visto que na
operação de colheita, com colhedoras automotrizes, todos as sementes são colhidas,
isto é, não há seletividade, faz-se necessário que a cultura seja homogênea,
não só quanto à maturação, mas também no que diz respeito ao porte das plantas,
percentagem de desfolha e declividade do terreno.
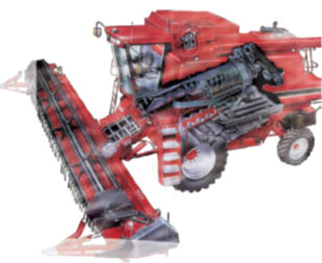
A uniformidade da lavoura inicia na escolha da variedade a ser
cultivada, passando por operações importantes, como sistematização do terreno,
preparo do solo, semeadura e tratamentos culturais.
As
modernas colhedoras exigem também habilidade dos operadores, pois são máquinas complexas e estes devem estar capacitados para
desempenhar diversas tarefas, as quais são: condução da máquina, suas
regulagens, verificação de possíveis falhas durante a colheita, manutenção e controle
de equipamentos eletrônicos. Tais fatores evidenciam a necessidade de o
operador ser uma pessoa calma, observadora e, ao mesmo tempo, dinâmica e
capacitada.
Sabe-se
que a falta de observação, principalmente por parte dos operadores, das
recomendações de manutenção e regulagem dos fabricantes de colhedoras, é a
principal responsável pela paralisação e perdas na colheita, devido às falhas
na máquina. Portanto, para obter-se uma correta regulagem da colhedora, o que
certamente levará a um nível baixo de perdas na colheita, se faz necessário, tanto
ao operador da máquina quanto ao administrador da lavoura, o conhecimento das
características construtivas, seus diferentes sistemas e maneiras de adequar-se
sua regulagem à cultura que será colhida.
Até o
século IX, a colheita de grãos era essencialmente manual e a trilha do produto
colhido executada com manguais manuais ou por meio do pisoteio de animais. Na
metade deste século, foi inventada a primeira segadora de grãos, movida por
cavalos, e instalou-se a primeira fábrica de trilhadoras nos EUA. Em 1930,
surgiram as chamadas máquinas combinadas,
isto é, que fazem o corte e a trilha ao mesmo tempo. Já no ano de 1938, as colhedoras
automotrizes começaram a ser utilizadas da maneira como se conhece atualmente, ou
seja, fazendo as suas cinco operações básicas, que são o corte, a trilha, a
separação, a limpeza e o armazenamento.
Até
1977, o sistema de trilha das colhedoras permaneceu o mesmo (fluxo transversal), mas nesse ano, com a colhedora modelo 1440,
da International Harvester, introduziu-se um novo conceito para o sistema de
trilha dos grãos, chamado de sistema
de fluxo longitudinal,
popularmente conhecido como “fluxo
axial”, no qual o
cilindro e o côncavo encontram-se, normalmente, posicionados longitudinalmente
à máquina, fazendo com que o material a ser trilhado desloque- se na direção
paralela ao eixo do cilindro de trilha (normalmente denominado de rotor).
Durante
a colheita mecânica, as operações desenvolvidas na unidade de trilha e separação
têm por função destacar os grãos das partes da planta que os contêm, separando-
os dos restos da cultura (caule, espigas, vagens, panículas e folhas). A percentagem
de separação nesta unidade encontra-se, normalmente, entre 60% e 90%. Isso significa
que quase a totalidade dos grãos são separados dos restos da cultura na unidade
de trilha e separação.
No
sistema de fluxo longitudinal, o rotor – um
ou dois conforme o fabricante – é provido de aletas dispostas na sua periferia,
formando uma espécie de helicóide (caracol). O côncavo compõe-se por um
cilindro fixo, ou metade deste, de chapa perfurada, o qual circunda o rotor,
total ou parcialmente. À medida que o material (grão + palha) vai sendo
deslocado dentro do sistema, os grãos vão sendo liberados da palha, passando
através dos furos do côncavo. A palha fica retida, por um período de tempo
maior do que os grãos, sendo liberada para o exterior da máquina na extremidade
oposta à de alimentação.
Os
grãos, após saírem do sistema, são liberados numa coluna de ar e/ou sobre
peneiras, para que ocorra a limpeza final. Máquinas dotadas deste sistema não
possuem unidade de separação (saca-palhas), pois o mecanismo realiza ao mesmo
tempo a operação de trilha, separação e descarregamento da palha. Este fato,
por si só, já permite que as perdas de grãos sejam reduzidas, quando comparadas
às do sistema convencional. Além do que, permite a construção de máquinas com
menor número de peças móveis, portanto mais simples, leves e curtas.
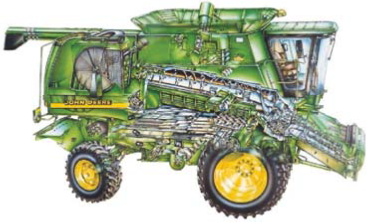
Sistema John Deere
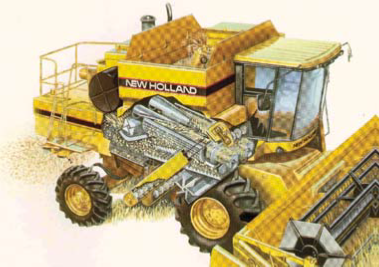
Sistema New Holland
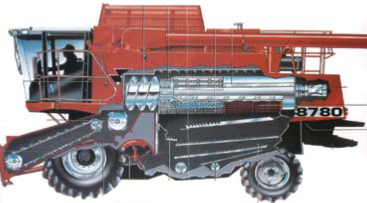
Sistema Massey Ferguson
Informações
de pesquisas dão conta de que o grau de danificação da semente colhida reduz-se
sensivelmente, quando se utilizam máquinas equipadas com o sistema de trilha de
fluxo longitudinal. Tal fato deve-se ao maior período de
tempo que o material permanece na seção de trilha, bem como devido a esta não
ser tão agressiva quanto a do sistema convencional. Portanto, máquinas dotadas
com este tipo de mecanismo são indicadas para a colheita de sementes ou grãos mais
sensíveis à danificações mecânicas.
Existem
diferentes sistemas que compõem o mecanismo de trilha longitudinal, os quais
apresentam variações de projeto em função do fabricante. No mercado nacional
tem-se disponíveis, atualmente, o sistema Axial Flow, da Case-IH ; o STS, da
John Deere; o Twin Rotor, da New Holland,; e o Rotari Axial, da Massey
Fergunson O sistema Axial Flow, da Case-IH, compõe-se de um rotor com duas
aletas propulsoras graduadas, que tem a função de conduzir o material colhido entre
o rotor propriamente dito e o côncavo. Este rotor possui vários elementos de
trilha, os quais encontram-se distribuídos, externamente, em forma de helicóide
ao seu redor. Os defletores envolvem o rotor em 360o, sendo divididos em
segmentos não contínuos, o que proporciona um fluxo mais rápido de material.
Após o material ser trilhado e separado, isto é, depois de sua passagem pelo
côncavo, ele é conduzido por meio de vários sem-fins até o sistema de ar e
peneiras, cuja finalidade é promover a sua limpeza. A palha restante é direcionada
para a porção final do rotor, sendo posteriormente jogada para fora da máquina.
O
sistema STS ,da John Deere , apresenta o módulo responsável pela trilha e
separação (rotor) dividido em três seções: seção de alimentação, de trilha e de
separação. Cada seção apresenta um diâmetro diferente, fazendo com que este
rotor fique descentrado em relação ao côncavo, o que, segundo o fabricante,
diminui a danificação provocada ao grão, quando comparado aos equipamentos
similares. A alimentação de material dá-se através de dez aletas, as quais
estão localizadas na extremidade inicial do rotor. A trilha é executada por
meio de três linhas diferenciadas, as quais contam com cinco elementos, que
possuem a superfície arredondada, cuja finalidade é proporcionar uma trilha
suave e progressiva. Na seção de separação existem 24 pinos (dedos)
separadores, cuja função é remover a palha, liberando os grãos a passarem
através das grades do côncavo. Existe ainda um módulo responsável por uma ação
extra de separação do grão que ainda esteja preso à palha, denominado módulo de
separação final, o qual é responsável por uma nova ação de separação, conduzindo
posteriormente a palha para fora do módulo “STS”, uniformizando o fluxo de
material para o picador de palha. O material trilhado e separado que passa
através do côncavo é conduzido por meio de semfins até o sistema de limpeza da
máquina, constituído por um sistema de ar e peneiras.
O
sistema Twin Rotor, da New Holland, é composto de dois rotores “geminados”, que
trabalham sincronizados, girando em sentidos opostos. Segundo o fabricante, o
sistema de dois rotores proporciona uma melhor alimentação, com maior força
centrífuga e menor peso, possibilitando uma trilha mais suave e melhor
separação. Os côncavos ficam paralelos aos rotores, proporcionando uma
repartição uniforme do material a ser trilhado.
Cada
rotor é dividido em três seções, que são: seção de alimentação, composta por um
helicóide, cuja função é promover o fluxo de material do canal alimentador da
colhedora até a seção de trilha e separação. Esta seção é composta de
raspadores e pinos (dedos) dispostos em formato helicoidal ao redor da
superfície externa do rotor, sendo responsável por 90% da trilha e separação do
material. Os restantes 10% são separados na porção final do rotor (seção de
separação), a qual compõe-se de vários pinos e aletas, ambos dispostos
helicoidalmente ao redor do rotor. As aletas da seção de separação, devido a
sua função, apresentam formato diferente daquelas da seção de trilha, sendo
mais compridas e de menor altura. Depois de trilhado, o material cai, através
do côncavo, diretamente sobre a seção de limpeza, constituída de um sistema de ar
e peneiras. O restante do material, composto de palha e grão que não foi totalmente
trilhado, é conduzido para a parte posterior do rotor, de onde é jogado sobre
um batedor de descarga responsável pela separação final do material e colocação
da palha para fora da colhedora.
O
sistema Rotary Axial, da Massey Fergunson, é composto por um rotor, o qual
possui na sua extremidade inicial um helicóide (caracol), cuja função é
promover a alimentação do sistema de trilha e separação. O material é então
conduzido por este helicoide até a área de trilha, a qual compõe-se de barras
raspadoras, situadas em torno da porção inicial do rotor, semelhantes às de um
cilindro de barras convencional, cuja função é promover o atrito do material
com o côncavo, possibilitando que os grãos venham a soltar-se da palha. O
material (grão e palha que ainda não foram trilhados), após passar por este
primeiro conjunto de barras raspadoras, é conduzido para trás, devido a
existência de pás fixas, as quais são colocadas em ângulo ao redor do rotor.
Estes elementos, em conjunto com as barras circulares do rotor, através da
geração de uma força centrífuga, permitem que ocorra a separação dos grãos que
ainda encontram-se unidos à palha. Na porção final, existem grades de
separação, colocadas num ângulo de 180º de envolvimento do rotor, que permitem a
separação final do material. Grãos e palha miúda que passam pelo côncavo e
grades de separação são conduzidos à seção de limpeza, composta de um sistema
de ar e peneiras.
Resumo:
Embora a
tecnologia das colhedoras com sistema de trilha e separação longitudinal exista
há mais de 25 anos, no Brasil este tipo de máquina passou a ser utilizado
recentemente,sendo em que todos os grandes fabricantes possuem um modelo
próprio. Como neste tipo de máquina o material a ser trilhado não necessita
mudar de direção, ao entrar em contato com os mecanismos de trilha e separação,
esta se dá de maneira mais suave. Tal fato proporciona um menor índice de
danificação mecânica ao material colhido, proporcionando, assim, sementes com
maior qualidade fisiológica. Além do que, a utilização deste sistema permite a construção
de máquinas com menor número de peças móveis, portanto mais simples, leves e
curtas.
Colaborou
com esta matéria Mauro Fernando Ferreira, professor da UNISC.